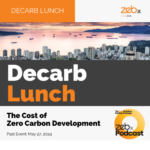
May 2024 Decarb Lunch: The Cost of Zero Carbon Development
May 28, 2024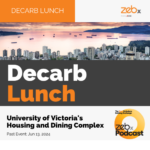
Jun 2024 Decarb Lunch: University of Victoria’s Housing and Dining Complex
June 17, 2024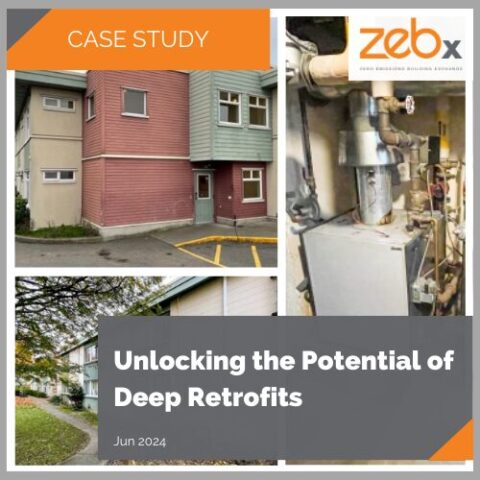
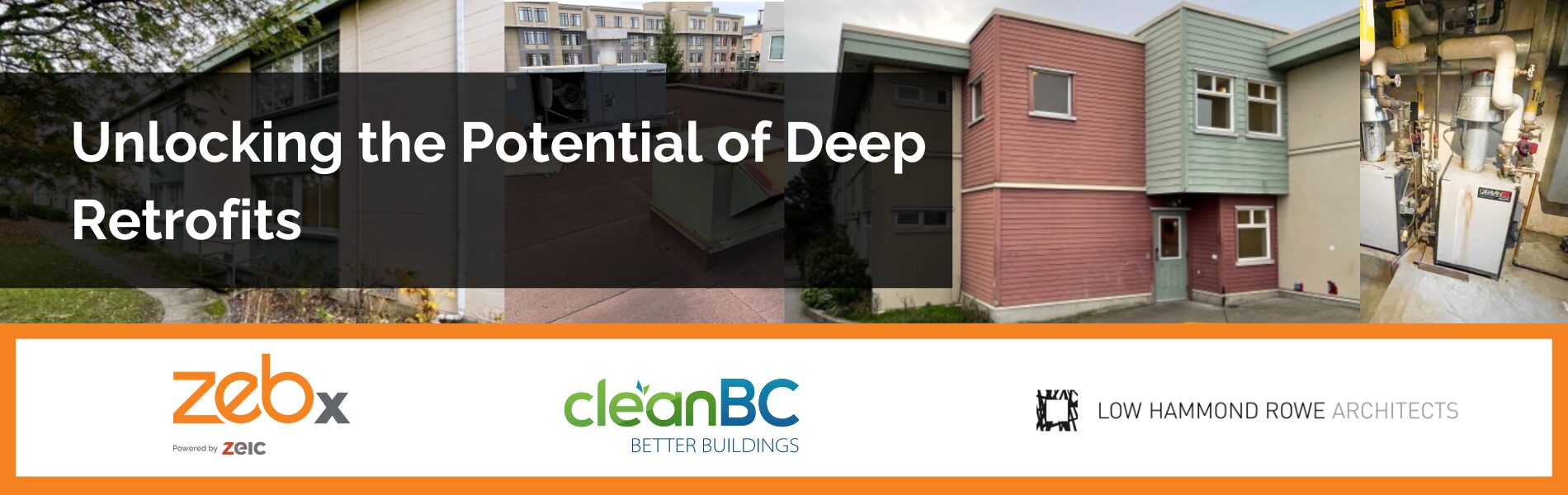
Lessons from Victoria’s Medewiwin Apartments
May 2024
It won’t be possible to meet municipal, provincial and national GHG emissions targets by simply building new energy-efficient or all-electric buildings. We need to decarbonize existing buildings too, and we need to do it quickly.
In British Columbia, the fact that about ¾ of the existing housing stock is projected to still be in use by 2050 underscores the crucial role of deep retrofits in meeting these targets. Although buildings account for 11% of the province’s total emissions (not including embodied emissions), they account for over half of GHG emissions in more densely populated urban centres like Vancouver and Victoria. This is almost entirely because gas is used so extensively for heating and hot water.
Low Hammond Rowe Architects’ (LHRA) involvement with the Reframed Lab, an initiative by the Pembina Institute, focused on deep retrofit schematic design solutions for Victoria's Medewiwin Apartments. This 26-unit supportive housing complex provides shelter to formerly homeless and at-risk residents. It comprises an original three-storey section from 1963 and a two-storey extension built in 2002. The 1,346 m 2 building produces significant GHG emissions, has poor energy performance and weak climate and seismic resilience.
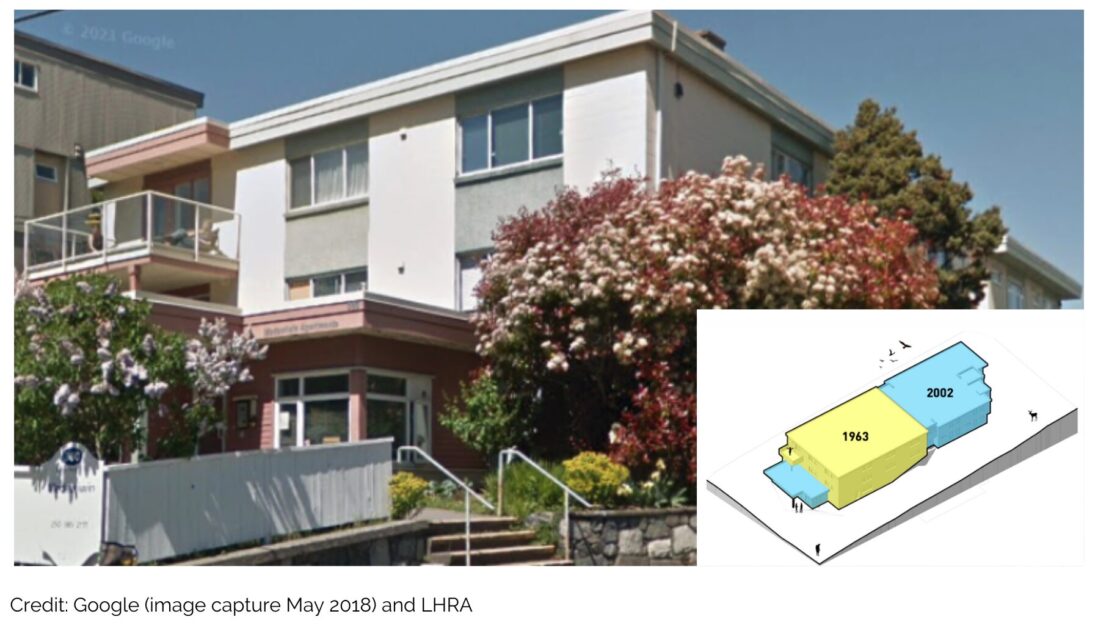
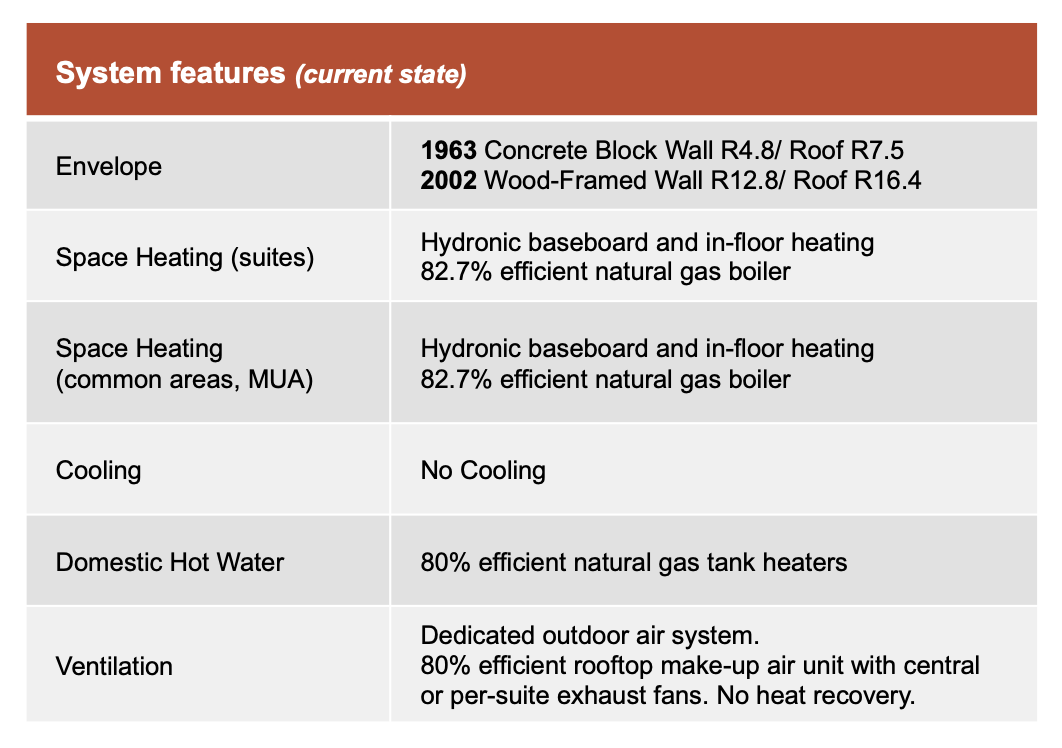
Achieving Interdisciplinary Synergy
In contrast to a traditional hierarchical design approach guided by standard practice and past experience, the Reframed Initiative employed an integrated design process guided by modelling and costing data generated early in the schematic design phase. The resulting interdisciplinary synergy helped the team better manage the complexity of generating and evaluating deep retrofit options. This approach promises to be a key enabler for the critical task of scaling up deep retrofits.
The ability to carry out comprehensive whole-building retrofits is heavily influenced by the alignment of design objectives among the design team: energy efficiency, decarbonization, seismic resilience and climate adaptation. To achieve this alignment, the design process was structured as a series of internal and external workshops to foster information and knowledge exchange among the design teams and the client.
The Integrated Design Team
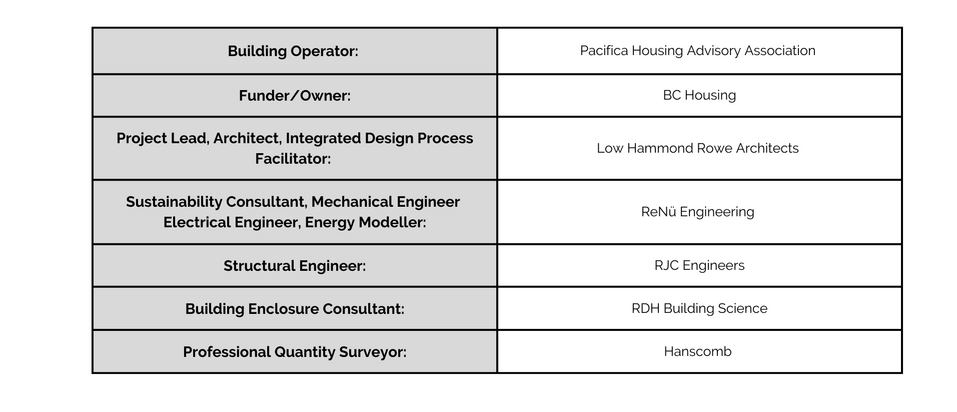
The design process followed a methodical evaluation of environmental, social, and financial factors to validate a retrofit approach.
The main objectives included:
- reduction of energy consumption and GHG emissions
- enhanced climate and seismic resilience
- improved tenant health and wellbeing
- maximizing the building’s net present value
The feasibility of adding an additional floor or extra rentable space, adding on-site electricity generation and storage, and improving aesthetic aspects were also considered.
The criteria for evaluating the options included:
- construction-related impacts on vulnerable tenants
- the needs of the building operator
- embodied carbon
- durability
- funding options
- price-performance ratios
- upfront and operational costs
- market maturity
- replicability for other buildings
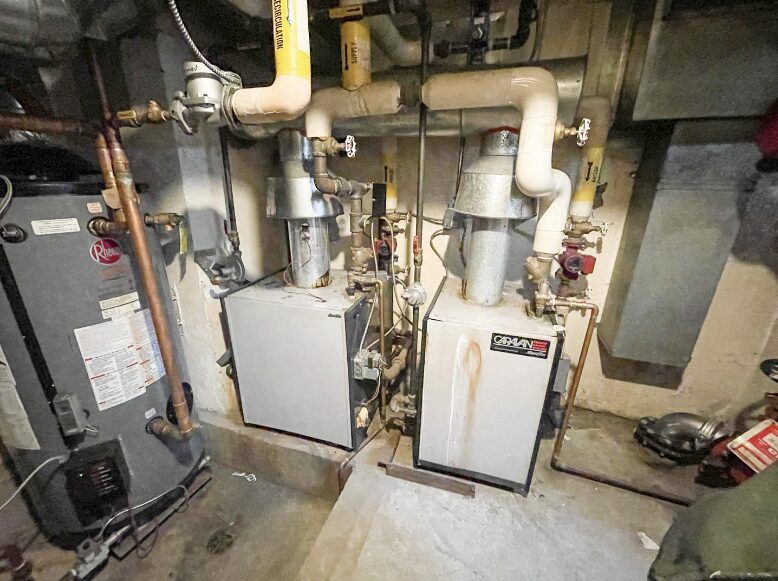
The Reframed Lab deliverables included two baselines of the existing building (existing performance and a ‘business-as-usual’ upgrade), four studies comparing different combinations of retrofit measures, and a schematic design on a recommended bundle of retrofit measures.
Each study included a:
- Class C capital cost estimate and lifecycle cost analysis
- climate resilience analysis
- seismic hazard/resilience analysis
- energy model
- thermal comfort analysis
- prefabrication feasibility analysis
- tenant vulnerability and risk analysis
- indoor environmental quality analysis
- accessibility analysis
For each of the four studies, the team selected a bundle of potential emissions reduction measures which were then modelled, analyzed and compared. Addressing the numerous design objectives and performance targets demanded a holistic approach while recognizing capital and lifecycle costs as critical design parameters. The team also aimed to build in flexibility to adopt newer, innovative systems or well-established technologies to suit market availability and cost factors.
Baselines and Bundles
Baseline A modelled existing performance using historical utility data. Baseline B reflected a typical business-as-usual retrofit with the replacement of energy-consuming equipment that would have reached the end of its theoretical service life within five years, and additional upgrades to achieve better compliance with the 2018 BC Building Code. The Baseline B scenario yielded a net present value increase of about 59%, as well as a decrease of about 18% in both GHG intensity (GHGI) and annual energy costs relative to Baseline A.
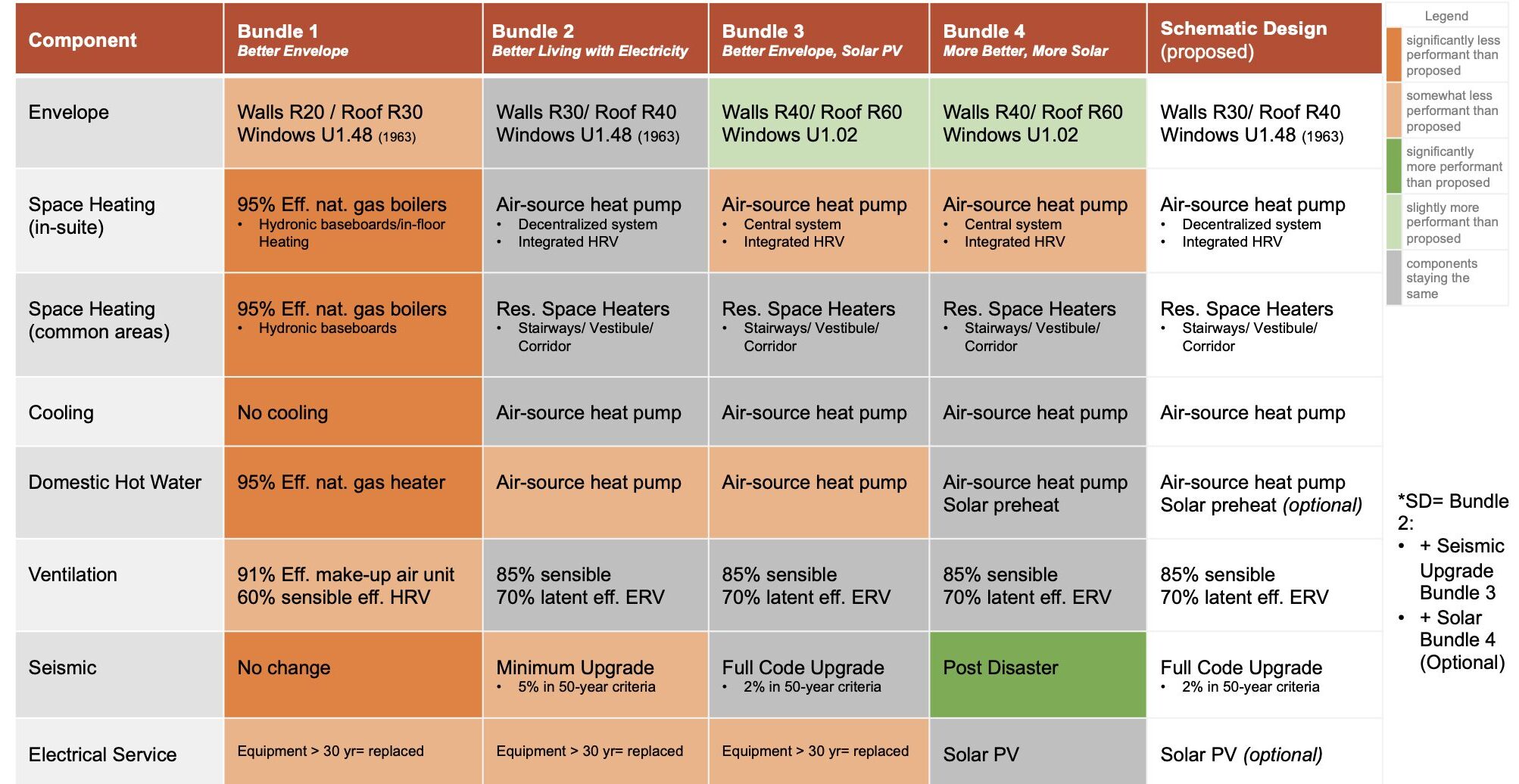
Bundle 1, “Better Envelope,” matched modest envelope upgrades with new, higher-efficiency gas-fired boilers and water heaters. The net present value of the building increased by 76%, the GHGI was reduced by 67% (23.6 kgCO2e/m2/year), and the annual energy cost was reduced by 52% relative to Baseline A. The capital cost was about 53% more than Baseline B.
Bundle 2, “Better Living with Electricity,” fully electrified space heating and domestic hot water systems and increased envelope and mechanical system performance. Climate resilience was enhanced by adding cooling and indoor air filtration. Some seismic upgrade work was included. The net present value increased by 86%. Elimination of gas-fired equipment reduced the GHGI by 98.6% (1 kgCO2e/m2/year). The annual energy cost remained the same as Bundle 1. The capital cost increased 65% over Baseline B.
Bundle 3, “Better Envelope, Solar PV,” further increased the performance of the envelope and mechanical systems, and added seismic upgrades for general compliance with the 2018 BC Building Code. Solar PV was added to further offset emissions. The net present value increased by 186%, the GHGI reduction was the same as Bundle 2, and the annual energy cost was reduced by 55% relative to Baseline A. The capital cost was about 178% more than Baseline B.
Bundle 4, “More Better, More Solar”, included the most energy-efficient envelope and mechanical systems. Solar preheating for domestic hot water was added. The net present value increase and capital cost increase were about the same as Bundle 3. The GHGI was reduced by 99.4% (to 0.4 kgCO2e/m2/year) and the annual energy cost dropped by 83% relative to Baseline A.
Proposed Schematic Design
After the four bundles were evaluated, a best-value schematic design was proposed combining elements of Bundles 2 and 3. The double-glazed windows in the 2002 addition were retained.
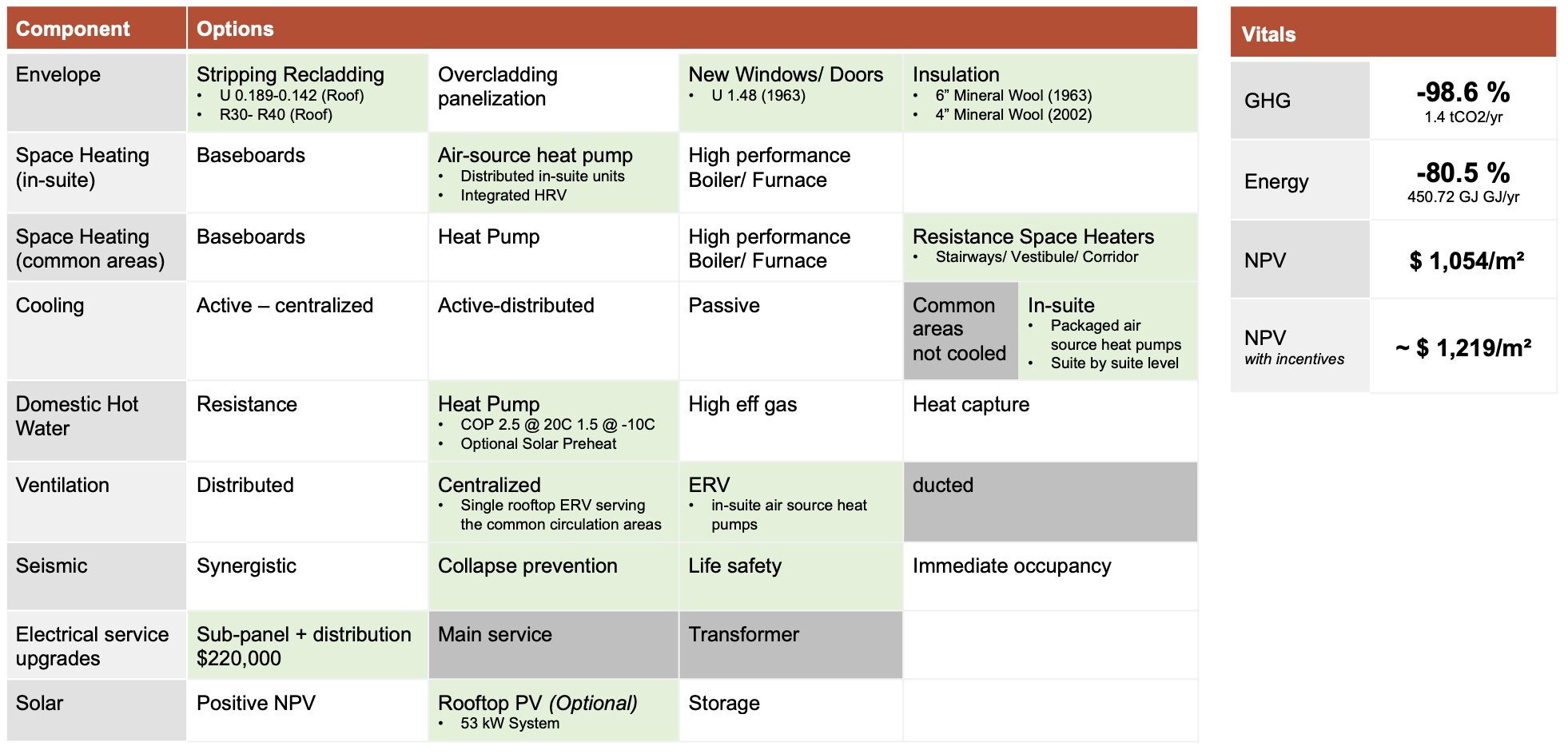
For heating, cooling and ventilation, a packaged unit (energy recovery ventilator with an integrated heat pump) was proposed for each suite, minimizing construction work in common areas and disruption of residents’ routines. The targeted energy efficiency for the ERV was 85% (sensible) and 70% (latent). Domestic hot water was to be provided by a centralized air-source heat pump.
Passive cooling measures (such as solar shading) were not included in the proposed design because the energy modelling confirmed that for Victoria's climate, the reduction in cooling load during summer was counterbalanced by an increase in valuable solar gain during the colder months. The window-to-wall ratio of the building is quite low. As a result, window performance was not a significant factor in overall performance.
Climate resilience was improved with mechanical cooling and air filtration. Better seismic resilience was achieved in a straightforward manner, meeting 2018 BC Building Code requirements for a modest cost. The installation of PV panels was left up to the owner given the additional upfront capital cost and associated payback period, the minimal impact on GHGI and the simplicity of adding this feature to the building independently in the future.
The capital cost for this proposed schematic design was estimated to range somewhere between the capital cost of Bundles 2 and 3. While the capital cost was approximated to be 72% more than the Baseline B retrofit, the GHGI would have been reduced by 98%, and the annual energy cost by 41%.
It's Not Just About Energy
There’s no question that a deep retrofit of an existing building is a more economical and expeditious alternative to new construction, considering not just the improvements in emissions and reduction in energy costs, but also the embodied carbon implications and the challenges of relocating tenants. Gaining approvals, designing and building new housing takes years, with ever increasing costs. Deep energy retrofits like this have the ability to achieve ambitious carbon emissions goals faster and more cost-effectively than new developments while preserving familiar social context and community character for residents and neighbours.
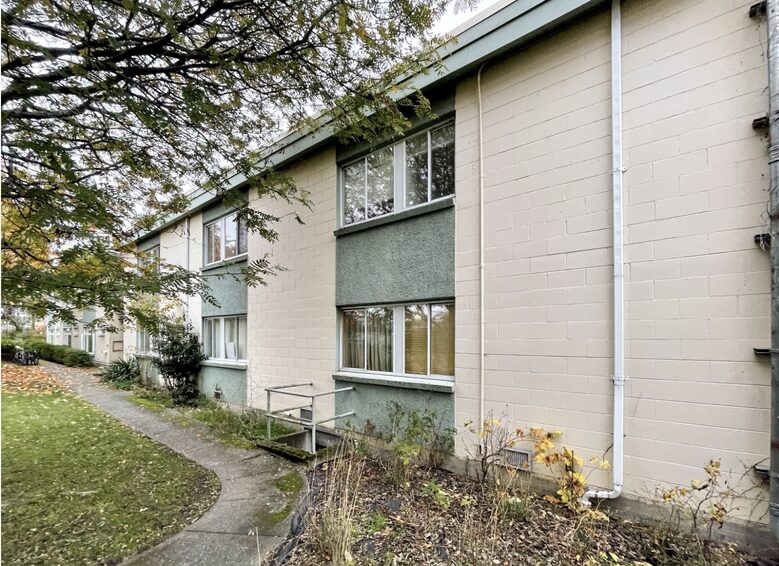
A deep retrofit can effectively mitigate community displeasure frequently associated with new developments. It does not require as much wasteful demolition and has a shorter duration and less intensive construction with less noise and fewer traffic disruptions. Compared to redevelopment, deep retrofits can help maintain the established identity of a neighbourhood. Reducing these impacts can decrease nimbyism and increase the likelihood of project acceptance by the community and municipality.
It is challenging, but clearly possible, to undertake a deep retrofit while keeping residents in place. Appropriate design choices, careful planning of construction sequencing, judicious use of off-site fabrication, and sensitive in-building relocation of tenants are essential strategies for achieving this goal. The vulnerable residents of the Medewiwin Apartments or similar supportive housing buildings are ideal retrofit clients: there are few options for them to move elsewhere, and their current home no longer meets basic comfort needs, but their strong emotional attachment to their home plays a crucially significant role in their mental well-being.
Written by Christopher Rowe and Jan Veselsky of Low Hammond Rowe Architects, and Roberto Pecora of the Zero Emissions Innovation Centre.
This article was written and published with funding from the CleanBC Building Innovation Fund.