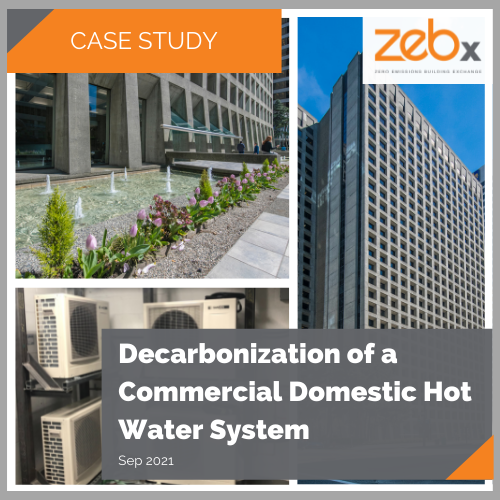
Decarbonization of a Commercial Domestic Hot Water System
September 15, 2021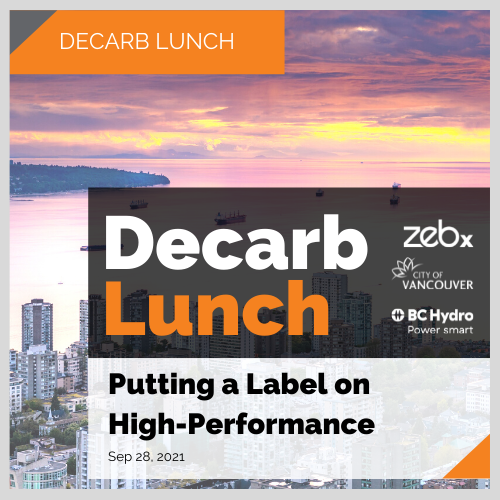
Sep 2021 Decarb Lunch: Putting a Label on High-Performance
September 28, 2021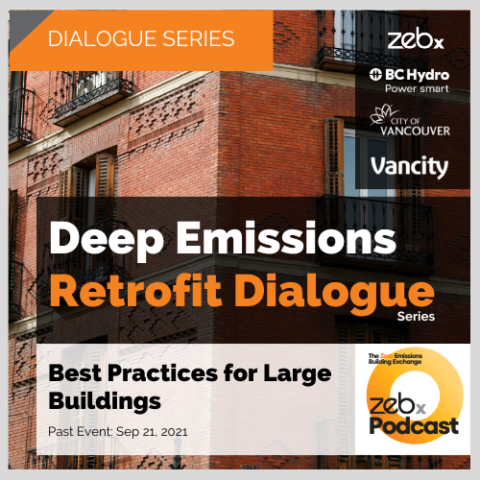
Deep Emissions Retrofit Dialogue One – Best Practices for Large Buildings
Recorded at Past Event: Sep 2021
Slides:
This event was a collaboration with the Building Owners and Managers Association of British Columbia (BOMA BC).
Summary
The biggest source of future operational emissions from the building sector will come from existing, rather than new
buildings. Retrofits which target massive reductions in operational emissions are essential to address the climate crisis
and will need to be scaled up dramatically over the next decade. In British Columbia, electrification is the most
effective strategy to achieve significant emissions reductions. This event was the first in a six-part series focused on
deep emissions retrofits.
Decarbonization of a Commercial Domestic Hot Water System
Presented by Nicky Arthur, Colliers
Arthur Erickson Place is a 26-storey office tower, constructed in 1968 and located in downtown Vancouver. The
presentation focused on a project that included the electrification of the majority of the building’s domestic hot water
heating system with an air-source, hot water heat pump system. Colliers, the property manager of the building,
explained that this project was the first step towards decarbonizing the building as a whole, in line with the building
owner’s sustainability objectives. It also provided ‘proof of concept’ for the building owners around this specific
decarbonization technology.
The project demonstrated the importance of aligning emission reduction goals with the building’s capital plan. It also
demonstrated that retrofits in older buildings are economically viable and play an important part in the transition to a
low-carbon economy.
For more information on this project, read our case study.
Barriers Presented:
- Asbestos abatement was required.
- Right-sizing of the system required more than just following American Society of Plumbing Engineers (ASPE) Guidelines.
- The initial GHG reduction cost and payback period were high.
Recommended Solutions:
- To reduce the payback period and GHG reduction cost, timing the project with the end of the service life of the existing equipment is critical. Financial incentives also play a key role in making a GHG reduction project more economically viable.
- The best outcome can be achieved when the various options are laid out ahead of time (like-for-like replacement vs higher efficiency vs all-electric option).
- It is important to consider that space will be required for both the heat pumps and storage tanks and in some cases (not this case), the electrical service capacity of the building or some of the panelboards may have to be increased.
- Locating heat pumps in warm areas helps make the heat pumps more efficient.
Achieving Deep Emissions Reductions in a 1968 Office Tower
Presented by Kenric Lee, Golden Properties Ltd.
The building located at 1177 West Hastings Street is also a 26-storey office tower in downtown Vancouver, built in 1968. In 2010, Golden Properties set a goal to eliminate the building’s GHG emissions and ultimately stop using gas entirely. They incorporated a decarbonization plan, centered on electrification, into their capital plan, and over the course of approximately ten years, they reduced their emissions by an impressive 70%, all while operating a fully occupied building. This is the kind of retrofit approach that B.C. needs – a studied, holistic and methodical approach of incorporating GHG-reduction measures into a long-range capital plan.
For more information on this deep emissions retrofit, read our case study.
Barriers Presented:
- Undertaking projects while the building was fully occupied.
- The building was designed with a high-temperature heating loop and the new heat recovery chiller could not provide hot water at the design temperature.
- The original design of the sixth-floor mechanical room did not consider replacement of the chillers.
Recommended Solutions:
- An integrated planning process involving the Operations Team, mechanical contractors and mechanical engineers enabled the most meaningful and best results.
- Adding an exterior access door to the sixth-floor mechanical room allowed a crane to remove the original chillers and lift in new ones.
- Energy conservation measures should precede electrification projects. This reduces the risk of exceeding the building’s electrical capacity and the capacity of some panelboards.
- Replacing the dampers on the air handling units resulted in more energy savings than expected.
- The original gas-fired boilers were kept to provide high-temperature hydronic heating on the coldest days of the year.
Deep Emissions Retrofit of a Multi-Unit Residential Building
Presented by Steven Fetterly, Impact Engineeering.
Semlin Gardens is a four-storey multi-unit residential building with 29 units. It was built in 1994 and is owned and operated by the YWCA Metro Vancouver.
Once the owner confirmed that parts of the building envelope and mechanical systems required renewal, they decided to explore cost-effective opportunities to combine GHG reduction measures with the renewal project.. As a result, they were able to achieve a massive reduction in operational emissions along with the renewal project.
Some of the electrification projects included:
- Replacing the gas-fired make-up air rooftop unit (for corridor ventilation and pressurization) with a hybrid gas/heat pump unit.
- Replacing the gas-fired boiler (for the low-temperature, in-floor, hydronic heating system) with a heat pump in the parkade.
- Replacing the gas-fired boiler (for domestic hot water) with a heat pump, also located in the parkade.
Installing the heat pumps in the parkade allows them to take advantage of slightly warmer air (than outside) which in turn, improves their efficiency and operating range. The low-temperature space heating system was well suited for electrification as well, since most available heat pumps designed for hydronic heating provide low-temperature water.
An electrical capacity analysis confirmed that there was spare electrical capacity that could be used for the electrification projects without requiring an electrical service upgrade.
For more information on this project see the video summary here or read the article here.
Barriers Presented:
- A complete upgrade of the building envelope was cost-prohibitive.
Recommended Solutions:
- An electrical capacity analysis should be done early in the planning stage to determine the extent of the electrification scope of work.
- Take advantage of the parkade to improve the efficiency and operating range of heat pumps. The cool discharge air can be ducted to the outdoors.
- A building envelope upgrade would not have provided the best return on investment for GHG reductions. Electrification of gas-fired mechanical systems proved to be more economically viable from a capital cost perspective.
- Older buildings often have underutilized space that can house the additional equipment that sometimes comes with electrification projects.
Presenters
Nicky Arthur, Energy & Sustainability Manager, Colliers
Nicky provides energy management and sustainability services to Colliers’ Real Estate Management Services across Western Canada. Expertise includes green building certification (BOMA BEST, LEED, WELL and Fitwel), utility monitoring and analysis using specialist software (consumption, costs and emissions for gas, electricity and water), waste management and tenant engagement.
Before joining Colliers, Nicky provided energy management and sustainability services for the Richmond School District, BC. She has also worked for over 10 years as an Environmental Consultant, primarily related to contaminated site investigation, risk assessment and remediation.
Kenric Lee, Director of Operations, Golden Properties Ltd
Kenric Lee is passionate about taking existing buildings through a journey of deep energy retrofits while primarily focusing on eliminating carbon emissions. He graduated from BCIT, School of Energy, Power and Process Engineering department in 2009 and holds a 3rd Class Power Engineer’s Certificate.
Kenric started operating and managing LEED certified buildings in 2006 and he was the Chief Engineer at Canada Place. In 2013 Kenric joined Golden Properties Ltd, where is continues as the Director of Operations with the family owned and operated real estate and development company located in Coal Harbour, Vancouver.
Steve Fetterly, Lead Energy Engineer, Impact Engineering
Steve is a Mechanical Engineer and Project Manager motivated to decrease greenhouse gas emissions. With a focus on the residential sector, he is experienced in designing high efficiency HVAC upgrades and implementing engineered solutions in projects across BC.
Steve works to deliver real energy and carbon savings in multi-unit buildings while improving system reliability and occupant comfort. He is a Professional Engineer and Certified Passive House Designer.
Hosts
Roberto Pecora, Director, ZEBx
Damian Stathonikos, President, BOMA BC